
How to Make Printable Fabric
Share
Do you have a favorite photograph (or two) that you'd like to incorporate in a quilt? Do you want to embroider one of the Anita Goodesign collections that use printed fabric? If so, you could buy sheets of paper-backed printable fabric. or you can make your own with a fabric of your choice. Commercially available printable fabric is certainly convenient but more expensive that fabrics you can prepare at home. In addition, commercial fabric printables are usually only found as white cotton. So why not make your own printable fabric? It's so easy.
You can use just about any smooth fabric you choose for this process, but keep in mind you want to be able to see your printed design. So, obviously, dark and some colored fabrics will not work. I personally just like to use off whites or tone on tone white fabric.
You can make printable fabric with silk as well as cotton, but I haven't tried it.


For best results, to keep your ink from fading or washing off, pretreat your fabric. The C. Jenkins Co. offers several options, depending on the type of printer you use. Follow instructions exactly or the prints may fade. Choose a product that's compatible with your printer inks, which can be either pigmented or dyes (or a combo of the two).
Krylon makes a product called Preserve It! that helps 'set' pigmented inks on fabric after printing.
The trick is to stablize your fabric so that it will go through your ink jet printer. To do this, I use waxed freezer paper as the substrate for the fabric. You can get a roll of the paper at the grocery store. Waxed butcher paper will also work.
The size of fabric you can print is limited only by the maximum dimensions that will feed through the printer. Cut the roll of paper into sheets the size of paper your inkjet printer can hold. I cut mine into 8½ x 11. If you have a printer that will take a larger sheet of paper, then you can, of course, cut the freezer paper to that size as well. It all just depends on what size you want your printed fabric to be.
Once you have the freezer paper cut to size, you can iron your fabric to it. Place the wrong side of the fabric on the waxed side of the paper. Use the hottest setting your fabric can take, and, with a dry iron, press the fabric to the freezer paper. I use a cotton setting on the iron for most of what I do. Adjust the iron temperature accordingly if you are using a different fabric like satin or silk. Iron until the waxed paper is firmly stuck to the fabric. Trim away any fabric hanging off the edges of the freezer paper.

Gloria Hansen offers excellent advice about the different types of inks used in printers, including a look at pigmented ink prints versus dye-based ink prints, and how the same images printed with each type of ink have weathered the years.
Once you have your fabric sheet ready to print, follow the instructions for your particular printer to manually feed the sheet into the printer. You will need to experiment with your ink jet printer to figure out the best settings to get the best print out. I use matte photo as my paper type and make sure the printer is printing "best" rather than "draft". Many printers have color adjustments you can make to make your colors more vivid, change to monochrome, etc. The possibilities are endless!
I printed a photograph on the marbled cotton and really like the added interest that it gives the photo.

Here is the same fabric printed with a line drawing from Anita Goodesign's "Autumn Bounty".

In the photo below, the white, tone on tone fabric really adds to the drawing from Anita Gooddesign's Birds of a Feather.
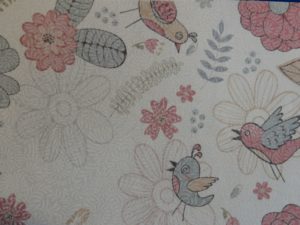
If you have a color laser printer, printing on fabric is similar to printing on an inkjet, except you needn't treat the fabric beforehand.
Because the toner can be thick, and the fixative adds more depth, laser printed fabric is stiff. So keep that in mind as you design your project. Use laser printed fabric for fabric postcards or designs used for wall hangings It also works well for items that can be machine quilted -- or don't need quilting at all.
Do you have favorite family photos? Make a quilt. Do you have travel photos? Print them out on printable fabric and make a beautiful wall hanging. Want to create your own fabric with a particular design? You can do it by making your own printed fabric. Experiment to find the methods and products that work best for your needs. We'd love it if you'd share your creations with us. Just click on the "Choose File" button below in the comments section.
How to Make Printable Fabric
The Fabric
You can use just about any smooth fabric you choose for this process, but keep in mind you want to be able to see your printed design. So, obviously, dark and some colored fabrics will not work. I personally just like to use off whites or tone on tone white fabric.
You can make printable fabric with silk as well as cotton, but I haven't tried it.


For best results, to keep your ink from fading or washing off, pretreat your fabric. The C. Jenkins Co. offers several options, depending on the type of printer you use. Follow instructions exactly or the prints may fade. Choose a product that's compatible with your printer inks, which can be either pigmented or dyes (or a combo of the two).
Krylon makes a product called Preserve It! that helps 'set' pigmented inks on fabric after printing.
Waxed Freezer Paper
The trick is to stablize your fabric so that it will go through your ink jet printer. To do this, I use waxed freezer paper as the substrate for the fabric. You can get a roll of the paper at the grocery store. Waxed butcher paper will also work.

Cut sheets
The size of fabric you can print is limited only by the maximum dimensions that will feed through the printer. Cut the roll of paper into sheets the size of paper your inkjet printer can hold. I cut mine into 8½ x 11. If you have a printer that will take a larger sheet of paper, then you can, of course, cut the freezer paper to that size as well. It all just depends on what size you want your printed fabric to be.
Iron the fabric to the freezer paper
Once you have the freezer paper cut to size, you can iron your fabric to it. Place the wrong side of the fabric on the waxed side of the paper. Use the hottest setting your fabric can take, and, with a dry iron, press the fabric to the freezer paper. I use a cotton setting on the iron for most of what I do. Adjust the iron temperature accordingly if you are using a different fabric like satin or silk. Iron until the waxed paper is firmly stuck to the fabric. Trim away any fabric hanging off the edges of the freezer paper.


Print the fabric
Gloria Hansen offers excellent advice about the different types of inks used in printers, including a look at pigmented ink prints versus dye-based ink prints, and how the same images printed with each type of ink have weathered the years.
Once you have your fabric sheet ready to print, follow the instructions for your particular printer to manually feed the sheet into the printer. You will need to experiment with your ink jet printer to figure out the best settings to get the best print out. I use matte photo as my paper type and make sure the printer is printing "best" rather than "draft". Many printers have color adjustments you can make to make your colors more vivid, change to monochrome, etc. The possibilities are endless!
Examples
I printed a photograph on the marbled cotton and really like the added interest that it gives the photo.


Here is the same fabric printed with a line drawing from Anita Goodesign's "Autumn Bounty".

In the photo below, the white, tone on tone fabric really adds to the drawing from Anita Gooddesign's Birds of a Feather.
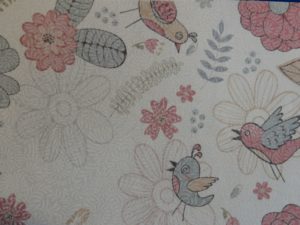
Laser printers
If you have a color laser printer, printing on fabric is similar to printing on an inkjet, except you needn't treat the fabric beforehand.
- Bond the fabric to freezer paper as explained above and run it through the printer's manual feed area.
- Leave the freezer paper attached to the paper and place the print on newspapers outside or in a well-ventilated room.
- Coat the fabric with several light layers of Krylon Workable Fixatif (or another similar product).
Because the toner can be thick, and the fixative adds more depth, laser printed fabric is stiff. So keep that in mind as you design your project. Use laser printed fabric for fabric postcards or designs used for wall hangings It also works well for items that can be machine quilted -- or don't need quilting at all.
Be creative
Do you have favorite family photos? Make a quilt. Do you have travel photos? Print them out on printable fabric and make a beautiful wall hanging. Want to create your own fabric with a particular design? You can do it by making your own printed fabric. Experiment to find the methods and products that work best for your needs. We'd love it if you'd share your creations with us. Just click on the "Choose File" button below in the comments section.